Виробництво пеллет і брикетів
Останнім часом з'явився величезний інтерес до виробництва твердого біопалива у зв'язку з різким подорожчанням газу і можливим скороченням подачі його споживачам.
Існує кілька методів переробки біомаси для отримання пеллет і брикетів. Я хочу поділитися своїм накопиченим досвідом у виробництві твердого біопалива. На першому етапі необхідно не помилитися з вибором технології переробки відходів біомаси.
Розрізняють декілька технологій виробництва пеллет і брикетів. Чим відрізняються пеллети від брикетів - це форма і розміри. Пеллети, як правило, мають циліндричну форму діаметром від 3мм до 8мм і довжиною від 5мм до 40мм. Брикети ж можуть мати циліндричну, прямокутну, овальну й інші форми, а розміри зазвичай складають: діаметр від 20мм до 100мм і довжина до 300мм. Я говорю про найпоширеніші розміри та форми.
Отже пеллети (гранули)
Пелети виробляють на грануляторах. Існує два основних види грануляторів - з плоскою і круглою матрицею.
Плоска матриця являє собою плоский металевий диск з високоякісної сталі діаметром від 100мм до 1250мм і товщиною від 20мм до 100мм. Сталь, з якої виготовляється матриця, повинна мати властивості підвищеної зносостійкості та можливістю загартування в межах 60 одиниць за шкалою твердості Роквелла. Зазвичай це вітчизняна сталь 40Х, шведська HARDOX 500, сталь 20CRMN або іншої марки.
Продуктивність гранулятора залежить від діаметра матриці. Гранулятори з матрицею діаметром 1250мм можуть видавати до 3 тонн пеллет на годину. Лідером у виробництві таких грануляторів є німецька фірма KAHL. Вартість такого гранулятора і периферійного обладнання до нього дуже і дуже висока. Я знаю кілька українських фірм, які витратили від 3 до 10 млн Євро на заводи з подібним обладнанням, але позитивних результатів за 3-4 роки майже немає. Виробництво пеллет - це дуже складне мистецтво. На такому обладнанні потрібна висока культура виробництва.
Другий вид - гранулятори з круглою матрицею з діаметром до 550мм. Матриця, як правило, виконується з нержавіючої зносостійкої сталі, яка калится до твердості 45-50 кгс по Роквеллу. Продуктивність таких грануляторів може досягати 3т / год.
Взагалі, коли ми говоримо про продуктивність, ми повинні диференціювати її величину від якості самої сировини, від її складу при ідеальній підготовці сировини перед подачею в гранулятор. Ще на продуктивність істотно впливає встановлена потужність електродвигуна. Брендові фірми, що випускають гранулятори, встановлюють редуктор з параметрами крутного моменту і передавальним числом з високим ККД, що дозволяє використовувати електродвигун з оптимальною потужністю.
Невеликі українські підприємства, як правило, встановлюють на гранулятор редуктор заднього моста вантажного автомобіля. На 90% китайських грануляторів встановлено такий редуктор. Це працює, але вимагає на 10-15% більше енерговитрат.
Гранулятори з круглою матрицею дуже давно застосовуються на території СНД для виробництва комбікорму. Це гранулятори серії ДГ і ОГМ. Наші умільці переробляють їх під виробництво паливних пеллет. Власне необхідно виготовити нову матрицю під потрібну сировину і ролики що її викочують. Принцип роботи однотипних грануляторів подібний.
Існує третій тип грануляторов мало поширений в СНД - це гібрид гранулятора з плоскою і круглої матрицею.
Кругла матриця розташовується формуюючими каналами паралельно до сонови, а вкочуючі ролики закочують сировину, що надходить до робочих органів гранулятора, під власною вагою. Така модель сьогодні дуже популярна в Китаї.
Периферійне устаткування
Новачки, які починають виробництво пеллет, як правило, не розуміють, що гранулятор - це 20% успіху виробництва пеллет. Дроблення, сушіння, тонке подрібнення, водопідготовка, змішування і дозування - ось ті процеси, без яких жоден гранулятор не працюватиме стабільно. Сировина, яка буде гранульованою необхідно особливо ретельно підбирати. По порядку.
60% бажаючих налагодити бізнес гранулювання хочуть переробляти деревину. Великі шматки деревини необхідно подрібнити до розміру тріски не більше 50мм. Це досягається залежно від розмірів різними машинами:
1. Горизонтальний тріскоріз (стаціонарний / мобільний)
2. Барабанна дробарка (стаціонарна / мобільна)
3. Шредер (стаціонарний)
Це обладнання суттєво відрізняється один від одного за ціною і продуктивністю.
Тріску потрібно просушити до вмісту вологи ≤ 10%. Це дуже непростий процес. Варто розуміти, що необхідно пов'язану вологу під впливом температури виділити із сировини у вигляді пари, а потім вентилятором видалити з сушильного пристрою.
Перше, що слід знати, і це є основа процесу сушіння, сировина до входу в сушку повинна бути з вологою ≤45%. При вмісті більш високого показника в сушці утворюється надлишковий пар, і процес випаровування сповільнюється до нуля.
Вважається, що вологість свіжо-зрубаної деревини 55-60%. Після тріскорізу вона повинна природно підсохнути, а потім її можна відправляти в сушарку. Або пропустити деревину двічі через сушку, що підвищує вартість сировини.
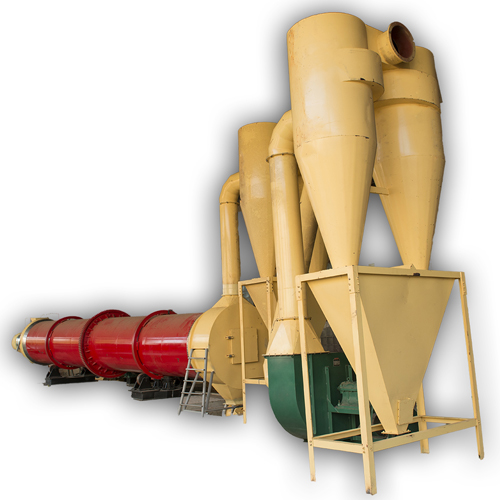
Чим менше ми залишимо вологи в сировині (≤10%), тим продуктивніше буде працювати молоткова дробарка, яка має дати фракцію рівну 1/2 діаметра каналу матриці. Так, якщо ми робимо пеллету діаметром 6мм, то фракція повинна бути ≤3мм.
Після молоткової дробарки необхідно підготувати сировину в змішувачі-дозаторі. Тут треба зволожити сировину приблизно до 14% залежно від конструкції гранулятора, якості сировини та рівень вологи підбирається експериментально. Сировина в гранулятор подається дозовано.
Параметри, що впливають на роботу гранулятора:
1. Глибина формуючих каналів матриці підбирається для кожної сировини індивідуально. Довжина каналу впливає на щільність гранули.
2. Фаска на вхідному каналі матриці (зенькування) підбирається під кожну сировину.
3. Форма та діаметр вкочуючих роликів підбирається по сировині.
4. Обороти головного валу гранулятора, як правило, лежать в межах 80-120 об/хв або швидкість роликів повинна бути 2,2-2,7 м/секунду.
5. Конструкція пристрою не дозволяє підніматися легкій сировині від площини матриці (для грануляторів з плоскою матрицею).
6. Потужність двигуна впливає на продуктивність гранулятора. Чим жорсткіша сировину, тим потужніший потрібен електродвигун.
Сировина для гранулювання
Найчастіше телефонують люди, які починають бізнес гранулювання, з приводу гранулятора. На питання про те, яку сировина вони збираються гранулювати, мені відповідають, що є частина деревних відходів, солома, некормові відходи с/г і т.д. Тобто існує некомпетентна думка, що в гранулятор можна кидати, все що завгодно і отримувати гранулу. Скажу відразу - 95% бажаючих виробляти зміксованому гранулу потерпить фіаско від такої затії.
Мої колеги з Умані вже багато років займаються гранулюванням соломи. Вони мені розповіли, що солома одного і того ж сорту пшениці з різних полів гранулюється по-різному. Буває так, що з певного поля і зовсім не гранулюється.
Гранули (пелети) виробляють двох видів: для промислового використання та побутові за європейськими стандартами.
Перші використовуються в промислових печах і топках. Найчастіше їх подрібнюють на порох перед використанням, а потім подають в пилові топки. Так роблять на польських ТЕЦ.
Побутові гранули дорожчі у виробництві, але користуються попитом у Європі. Виготовляються пеллети діаметром 6мм з хвойних порід деревини з попереднім очищенням від кори.
Хочу запропонувати кілька груп сировини для гранулювання:
Легко пеллетовані
1. Сіно люцерни
2. Суміші зернових
Пеллетовані
1. Деревина хвойних порід
2. Відходи коробочки сої
3. Відходи сочевиці
4. Лушпиння соняшника
5. Солома сої
Погано пеллетовані
1. Змішані відходи с / г
2. Листяні породи деревини
3. Лігнін
4. Торф
5. Суміші біомас
Нерекомендовані
1. Лушпиння рису (висока абразивність, низька теплотворність, висока зольність)
2. Деревина фруктових дерев, виноградна лоза (висока абразивність, вимагає високої міцності обладнання, зпікаємість при згорянні).
Найчастіше хочуть переробляти те, що бачать, наприклад, очерет. Зазвичай я пропоную прибрати 0,5га плантації очерету, зважити його, порахувати собівартість прибирання, і вже не захочеться його гранулювати.
Ми повинні розуміти до чого ми прагнемо. Наша кінцева мета - це продати наш продукт і отримати прибуток. Перш ніж почати цей бізнес необхідно знати, скільки і яку сировину ви зможете використовувати, кому і яку кількість ви зможете продати. Після аналізу підібрати обладнання і скласти бізнес-план.
Ще раз скажу, що гранулювання біопаливних гранул дуже складний процес. Перш ніж ви почнете цим займатися, відповідально підійдіть до цього питання, все прорахуйте.
Брикетування
На мій погляд, брикетування більш простий спосіб отримання біопалива. Брикет - це продукт заміщення вугілля, і в даний час він дуже затребуваний на внутрішньому ринку України.
Існує 5 основних способів виробництва брикетів:
1. Ударно-механічний - Нільсен (Nielsen)
2. Екструзійний з температурним нагріванням - ПініКей (Pini & Kay)
3. Гідравлічний типу РУФ (RUF)
4. Кільцевій
5. Екструзійний холодний спосіб.
Одним з розповсюдженний способів виробництва брикетів є ударно-механічний. Принцип роботи - кривошипно-шатунний механізм приводить в рух поршень, який з великою частотою б'є по сировині, що подається у вихідну головку шнековим дозатором. Вихідна головка має таку форму, що дозволяє формувати брикет потрібної циліндричної форми. На виході брикет підпирається або гідравлічним способом, або механічним. У більшості випадків ділянки лінії руху брикету від головки до ділянки складування складає більше 10 метрів.
Лідером серед верстатів для виробництва таких брикетів є датська фірма CFNielsen, чиє обладнання може досягати потужності до 1,5 т / год. Технологія вимагає дуже хорошу підготовку сировини (волога, фракція, однорідність) і бажано окорковані хвойні породи деревини. Обладнання цієї компанії дуже дороге - близько 500.000USD. Такий тип пресування широко використовується в Індії та обладнання цієї країни має непогану якість.
Брикетер екструзійний Pini & Kay з нагріванням поширений в Україні завдяки низькій вартості від 2000USD до 4000USD. Брикет виходить дуже гарний і щільний з отвором всередині. Але на цьому закінчуються всі плюси даного методу виробництва.
Для отримання брикету сировина повинна бути висушена до показника вологи менше 8%, що досить проблематично. Недоліком технології є необхідність подрібнення сировини до дрібної фракції, а також дуже низька продуктивність - від 50кг / ч до 200кг / год. Через кожні 6-8 годин роботи необхідно заробляти шнек екструдера зносостійкими сплавами. В результаті виходить дуже висока собівартість брикету.
Брикет типу РУФ виробляють на гідравлічних пресах німецької фірми RUF, латвійської RMP та польської BIZON. Тиск у таких верстатах створюється до значення 300 бар. Для продуктивності 400 кг/год необхідно формувати брикет 15х6х11мм. Такий продукт на ринку України не має масового попиту через великий розмір. Крім того волога сировини повинна бути менше 14%, а фракція менше 3мм. Хоча ці преса найнадійніші з усіх видів даного обладнання для виробництва брикетів, але дуже дорогі - від 48000 € до 100 000 €.
Ще одним видом гідравлічних пресів є так звані преса Nestro, які випускає німецька фірма Nestro Lufttechnik GmbH. Вони відрізняються від пресів типу RUF тим, що протидіючою силою головного циліндра є вихідна головка з гідравлічним замком. Такі показники як низька продуктивність - в середньому 100кг / год, високі вимоги до підготовки сировини та висока вартість зробили цей прес непоширеним на території України, хоча брикети після цього пресу мають досить приємний товарний вигляд.
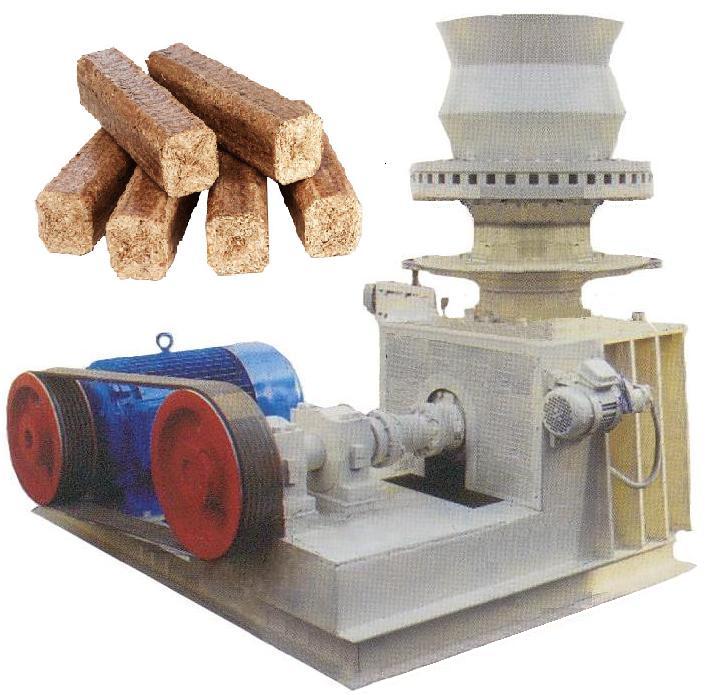
Брикет користується попитом у населення для обслуговування домашніх печей. Недоліком є необхідність досушування брикетів від 3 до 7 днів. Для цього готовий брикет на виході пакується в овочеві сітки та складується на піддони по 450кг. Піддони відстоюються 3-7 днів під навісом до вмісту вологи в брикетах до 16%.
Такий брикетер працює у виробничому цеху компанії «Зерма-Україна» Херсонської області на соєвій соломі. Готовий брикет має розміри в перерізі 32х32мм. В Україні подібних брикетерів немає. Обладнання коштує відносно недорого - 32000USD, а термін окупності складає 5 місяців.


Брикетер холодної екструзії - дане устаткування добре підходить для екструдування торфу, вугільного пилу, соломи сої, жирних відходів соняшника. Продуктивність від 1т/ч до 2,5т/год. На виробничому майданчику «Зерма-Україна» екструдер виробляє брикети діаметром 32мм з високою теплотворністю з відходів соняшника та соломи сої.
Позитивними факторами є низька настановна потужність 32кВт, немає необхідності сушити сировину, висока продуктивність і невисокі трудовитрати. А негативним фактором є необхідність додрібнювати солому через сито з діаметром комірки 8-10мм.
Коли я вам описував обладнання, я завжди говорив про вологу та фракції. Пам'ятайте, що периферійне устаткування таке ж важливе, як і гранулятор і брикетер.
Генеральний директор ТОВ «Зерма-Україна»
Гребенюк Петро Олексійович
М.т .: +38 050 418-52-02
Тел .: +38 05536 21402
www.tmgreenbull.com.ua
Гребенюк Петро Олексійович
М.т .: +38 050 418-52-02
Тел .: +38 05536 21402
www.tmgreenbull.com.ua